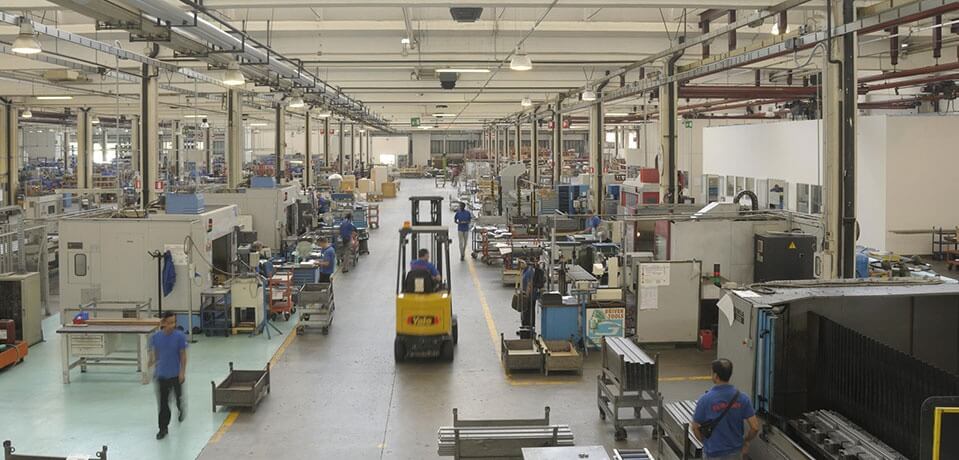
ROLLON GOES LARGE
ROLLON UPSCALES
Last month one of our team visited the excellent Rollon factory in Italy. The Rollon group has expanded and improved significantly over the last few years with increased capital expenditure. Their main factory is world class, well organised, highly automated and efficient. In the compact rail production line the operators spend most of their time doing quality assurance work with every batch being quality tested at set intervals at each stage of production.
Especially impressive is the automated straightening process. Hardening and quenching of the rail causes twisting due to the irregular shape of the rails. Every rail is measured for twist or out of plane and hydraulically twisted or bent back into tolerance completely automatically.
In the last couple of years Rollon has also acquired a number of related businesses and now have one of the world’s largest ranges of guided actuators. Their range includes roller or profile rail guided systems with rack and pinion, ball screw and belt drives.
Anodised aluminium bodies with integrated T slots are extensively used. The extrusions have been engineered for low weight and high strength. Extrusions are straightened and or machined to provide the required accuracy of the mounting surface for guide ways and drive systems.
Rollon’s large scale systems have serious capacities with profile and roller guidance systems reaching static capacities of over 10 tonne and stroke lengths of 10 meters or more. One customer uses Rollon for an integrated overhead gantry system handling entire washing machines through multi stations.
Systems can be properly engineered as dynamic life is stated on most models so a realistic service life can be assessed. High performance vertical omega drives with pneumatic counter balance and extensive pre-engineered interfacing is available to make a wide range of 2 and three axis gantry systems.
The precision TH system features a properly engineered ball screw with precision supports, twin profile rail, lubrication ports all in a sealed aluminium extrusion. Integrated bell houses can be supplied to bolt a motor straight on – precision motion with a minimum of design effort and on short lead times.
ELM types have and excellent sealing system for challenging environments. A polyurethane strip runs the length of the actuator. The edges of the strip are slotted and retained by a finger in the extrusion. Micro bearings in the carriage lift the strip from the finger and return it back into position as the carriage passes. Side seals and micro brushes complete the system to create an extensive barrier to dust and foreign matter.
We assemble the Uniline family of actuators from stock here in New Zealand and can integrate the entire range of Rollon actuators.
YASKAWA SERVO
Yaskawa’s commitment to the world’s highest performing motion is again displayed with their recently introduced sigma7 series. Encoder resolution in this family is now an astonishing 24bit or 16.7million pulses per revolution. This increased accuracy gives sigma7 unequalled precision, much reduced vibration and faster settling times. For the first time sigma7 is also available integrated with either of the world’s most popular motion networks – EtherCat or Mechatrolink.
We have Yaskawa servos and controllers in stock and are experts in the tricky job of servo sizing. Call or email us to discuss your application.
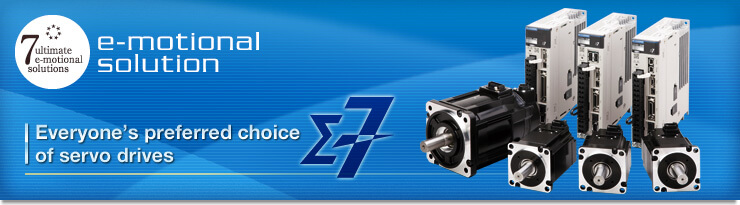